Walk past the newer apartment complexes and condos in the Twin Cities and you can tell something is wrong, even though you can’t pinpoint what. It can’t just be that these buildings all look the same, right? You notice something shabby about the exteriors, something makeshift, something off.
It’s not all in your head. You’re definitely on to something.
As the son of a lifelong siding man, I grew up on my dad’s regular lectures about the competition’s shoddy workmanship, so naturally the siding was where I first looked for defects in these new construction jobs. And even my far-from-expert eye could spot how many siding panels were prematurely warped or otherwise flawed.
According to Chris Knutson, a second-gen siding installer in the Twin Cities, the problem isn’t just the quality of installation work, but the siding itself.
“A lot of the materials they use and a lot of the techniques they use are new,” he says. “And that means the siding hasn’t been tested for wear, and many don’t know how to put it up.”
Knutson knows what he’s talking about. His father’s been in the siding business since 1974; he started working with his dad as a teen, then began installing full time seven years ago.
The siding style you're probably familiar with is lap siding. Made initially of aluminum and then more commonly vinyl, lap siding is installed in overlapping panels (hence the name) along horizontal rows, and its look mimics the wood exteriors it initially replaced. You know, this stuff:
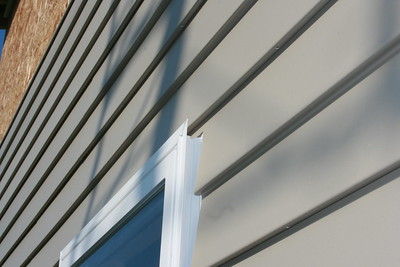
But now, Knutson says, you’re likely to see slot panel siding, typically made from engineered wood, steel, or fiber cement. You see it all over the notorious/ubiquitous "5-over-1"-style construction projects.
“People who want apartment remodels want it, but it sucks,” he says. He’s worked with it himself and seen its problems firsthand. “It’s not a great product, and it’s not really all that tested. So if you see it starting to fail now, it’s all going to be failing in 10, 20 years. And when these things start failing, people are going to have to replace the entire exterior.”
Water damage is the most common threat to panel siding installations.
“The reason that lap siding stood the test of time is that there are a lot of different areas for water to shed,” Knutson explains. “Now imagine a panel: There’s one point for it to shed. That’s where it will fail the most, and I can already see the beginnings of that.”
And it’s not just houses and condos that are using this material. One of the most notorious exterior design failures in recent Minneapolis history can be chalked up to an improper installation of panel siding.
“I don’t want to say it by name, I don’t want to get in trouble, but let’s say, there’s a stadium where people play football,” Knutson jokes cagily. “To me, the second I looked at that, and probably a lot of professionals thought this—my dad and I, we thought, well, that’s gonna fail.”
And as we all remember, the black metallic zinc siding that encases U.S. Bank Stadium did indeed begin to partially detach just six years after construction, resulting in a $21 million repair job.
“One issue is a lack of skilled labor,” Knutson says. “It is really hard to find good people.” Some construction companies "must be hiring people with less experience and maybe less care.”
But skill only takes you so far, because there’s just no room for error in the installation process. And, Knutson says, there will always be some error.
“No one will ever do a perfect job,” he says. “If a product needs to be installed perfectly, it will fail.”